Success Stories
Remote Diagnostics for Safe Pump Testing
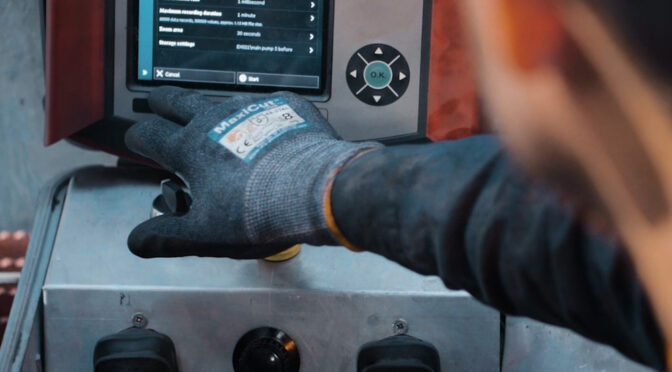
Background
To provide safe testing of large mobile plant hydraulic pumps, Glencore’s Clermont Coal Mine teamed up with Custom Fluidpower to design and manufacture a specialised, remote proportional control, flow test unit.
The Project
To conduct maintenance on a Hitachi EX 5600-6’s main pumps, a maintenance technician is required to undertake a hydraulic flow test on the machine while the machine is running at a low idle of approximately 980RPM.
In the past manual flow testers, comprising a flow meter with an inline restriction valve were required to conduct fault finding and maintenance. This required breaking into the system fluid connectors and risk potential contamination and fluid loss during the process.
A technician at Clermont was injured when he was conducting routine testing in the left-hand pump bay of the machine, adjusting the flow meter load pressure. The side housing of the flow meter had failed, allowing the fitting and thread for the delivery line to blow out the side of the flow meter, injuring the technician’s leg.
To avoid further safety risks, a remote proportional control, flow test unit was installation on the machine with a HYDAC HMG4000 handheld measuring device to collect and log hydraulic system data.
The HMG4000 is Custom Fluidpower’s preferred choice for hydraulic system recording or pressure, temperature, flow rate, and position.
The Results
Glencore’s Clermont Coal Mine are able to safely test pumps with a new proportional control flow unit accompanied by the HYDAC HMG4000, a handheld, portable measuring and data logging device whose main applications are field servicing, maintenance, fault finding and as a test rig data device, instead of using the manual flow tester method.
Client Outcomes
Remote pump control took the place of the manual valves and repetitive changing of hoses.
Control of pilot pressure proportionally to what is required, with the ability to turn on one pump, two or more, and other valves can control other functions.
The data logger can provide millisecond precise images, to grade all pressures, temperatures, and engine speeds, automatically executing calculations for flow rate versus pump speed making it much easier than adjusting the manual valve, allowing it to be set infinitely with a joystick away from the line of fire.
The HMG4000 data can assist in early intervention and the prevention of future catastrophic failures that inevitably contaminate the systems and cause unnecessary downtime. Pressure can be wound on and off the pump remotely in a much quicker way than if it were done manually by a technician at the pump.
Technicians can operate the control flow unit & HMG4000 remotely meaning they are no longer in confined work areas, adjacent operational, high-pressure hoses thus eliminating the risk of hoses trying to undo themselves and flow meters and lifting off the ground under pressure.
You can watch the case study on YouTube here.