News & Insights
Mobile and Off-Highway Equipment – Hydraulic System Optimisation
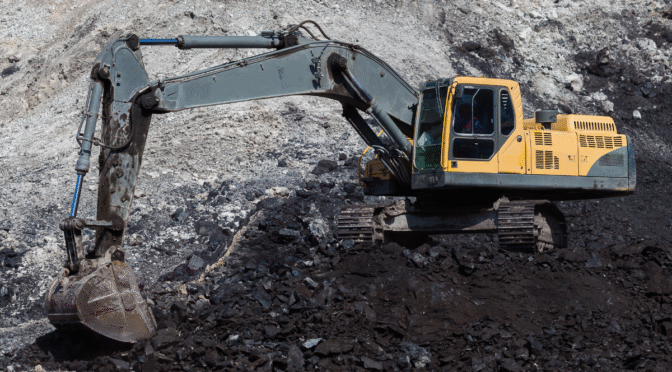
With the growing demands of industries such as mining, materials handling, construction and defence, optimising hydraulic systems performance is more crucial than ever for mobile and off-highway equipment. Known for its power density, hydraulics play an indispensable role in the operation of heavy machinery. These systems ensure that equipment like excavators, cranes, and drill rigs function smoothly and effectively, significantly contributing to the sectors they operate in.
In sectors like mining, equipment is exposed to rigorous conditions, requiring robust hydraulic designs to maintain reliable performance. The key to optimising reliability in these systems lies in smart component selection and ongoing maintenance. By ensuring each component is fit for purpose, tuned to the specific needs of the equipment, end users can achieve higher reliability and enhanced efficiency, even in the harshest environments.
Component Selection for Optimised Hydraulic Systems
Selecting the right hydraulic components is critical to achieving dependable system performance. Mobile equipment used in Australian industry requires its hydraulic system to cope with unique environmental factors and loads, and heat, vibration and external factors present unique challenges in relation to mobile equipment. When choosing hydraulic cylinders, for example, both operational durability and reliability must be considered. Drill rigs or excavators in mining applications demand cylinders that can withstand repeated heavy loads while maintaining precise motion control in harsh environments.
Equally important is selecting the correct hydraulic pump for the application. Pumps must align with the machine’s operational function – whether providing consistent pressure for cranes on construction sites or powering vital functions on agricultural equipment, such as sprayers. Performance characteristics such as flow rate, pressure rating, and mechanical and volumetric efficiency will determine whether the pump meets task requirements.
Hydraulic valves also play a critical role by managing fluid control within the system. Their operational performance and quality directly influence responsiveness and the operational safety of the machine. An incorrectly specified or poorly maintained valve can result in reduced system performance or costly downtime.
When selecting components, the following factors should be evaluated:
1. Load capacity specific to the application, such as pressure and flow requirements
2. Exposure to environmental factors like dust, pressure fluctuations, temperature extremes, and moisture. It is also important to consider exposure to flammable gases, which may require specific ratings for the components within the hydraulic system.
3. Integration and compatibility with current hydraulic systems
4. Maintenance demands over the equipment’s operational life
Making the right choices at the component level can combat operational inefficiencies, improve the working life of equipment, and reduce maintenance costs over time, even with the variability of working environment typical for this kind of equipment.
Enhancing Performance with Adequate Maintenance
Hydraulic system maintenance is central to machine performance. One aspect of maintenance is correct hydraulic fluid selection. The hydraulic fluid enables power transfer, component lubrication, and overall system cooling. Choosing the correct fluid ensures the system operates under optimal conditions and helps reduce wear. Depending on the application – for example mining conveyors, defence vehicles, or marine vessels – fluids must match environmental demands for viscosity, oxidation resistance, and anti-wear capabilities.
For mobile equipment operating in rugged Australian conditions, fluids that can handle high pressure and temperature swings are necessary. The wrong fluid often leads to seal damage, overheating, or reduced power output.
In tandem with fluid performance, filtration maintenance is critical to extending equipment life and avoiding unexpected faults. Scheduled checks of both fluid and filtration quality prevents minor issues from becoming system failures. Maintenance routines should include:
– Regular fluid analysis and replacement at appropriate intervals
– Inspection of hoses, seals, and fittings
– Filter replacements to maintain responsiveness and cleanliness
– Monitoring system pressure and temperature trends to identify faults early on
Establishing a routine servicing standard reduces downtime and improves operational readiness no matter what sectors the mobile equipment is operating in.
Advanced Hydraulic Solutions for Mobile and Off-Highway Equipment
In recent years, mobile and off-highway machinery have benefited from evolving hydraulic technologies. Hydraulic systems are now tailored for faster response, lower energy consumption, and easier system integration. These developments are especially beneficial for applications where machine control and power delivery need to be accurate and efficient.
Hydraulic accumulators are another critical development. By storing pressurised fluid, these units can absorb shocks, smooth pulsations, provide standby energy, and stabilise system operations. Their application in mobile equipment such as rail maintenance equipment, or agricultural machinery, mitigates hydraulic spikes and ensures smoother performance.
Through advanced hydraulic engineering, end-users now have access to custom-built systems that precisely fit the operational purpose of each machine. Whether enhancing braking in a wind turbine or bolstering load handling on a ship crane, these customised solutions add measurable value to performance and reliability.
Real-World Applications and Industry Impact
Hydraulic solutions are driving measurable increases in efficiency and safety across high-demand sectors. In Australia’s mining sector, for example, drill rigs equipped with properly calibrated valve systems and accumulator-supported pumps achieve faster cycle times and better energy management. Excavators using advanced fluid control maintain operational precision even in extreme climates, even when remotely controlled from hundreds of kilometres away.
Material handling operations also benefit. Forklifts and ship loaders now operate with reduced wear, fine-tuned control, and less fluid loss thanks to upgraded hydraulic setups. Similarly, automatic lubrication systems and custom cylinder designs are improving productivity in sugar mills and waste management units.
Green energy machinery, including wind turbines and renewable energy equipment, often depends on hydraulics for pitch control, slew motion, or braking actuation and lubrication. These applications demand high responsiveness and reliability – both of which are achieved through modern fluid circuits with accumulator support.
Marine applications frequently face salt exposure and continuous high-load use. Deploying corrosion-resistant hydraulic actuators and appropriately configured hydraulic valves ensures equipment continues to operate safely over long duty cycles.
Hydraulics is not just improving how each machine functions but also widening the scope of what these machines can achieve across Australia’s most vital sectors.
Why Industry Leaders Choose Custom Fluidpower
With operations across all states, Custom Fluidpower brings deep experience in designing, assembling, and servicing hydraulic systems across a broad range of industries. Our team supports mining exploration, agriculture, defence, marine, and green energy sectors by providing proven component solutions and custom system designs.
Our engineering-first approach ensures that mobile equipment gets the most efficient hydraulic configuration, driving measurable results. From initial consultation through to ongoing support, we help organisations adopt high-performing hydraulic technology suited to their real-world operational goals.
By investing in best-in-class components, relevant system upgrades, and regular maintenance programs, you protect your equipment, improve performance, and ensure that every hydraulic system is doing exactly what it’s meant to do – keep your operation moving productively and safely.
To improve the reliability and responsiveness of your mobile hydraulic systems, explore our range of engineering and design services. At Custom Fluidpower, we provide expertly engineered solutions designed to support demanding operations in sectors such as mining, materials handling, green energy, and transport. Our team delivers technical experience, tailored component selection, and dependable service across all states.